 |
|
|
ION SELECTIVE SCREENING: AT THE MOLECULAR LEVEL
The Metal Ion Barrier
A functional portion of the ion selective screening compound incorporated in the negative plate active material attaches end-on to the surfaces of the negative plate - covering the entire surface of the negative plate with bristles, generally as shown below. (The scale of the illustrations represents a magnification of about ten million times.)
The ends closest to the surface are in adsorption equilibrium, subject to attractive and repulsive electrostatic forces that act between the ion selective screening molecules and the surface, meaning there remains a tiny gap, (Reference 1.). This allows the battery related chemical reactions to proceed at the surface unimpeded and for the molecules to "ride" over the charging and discharging surface formations. |
|
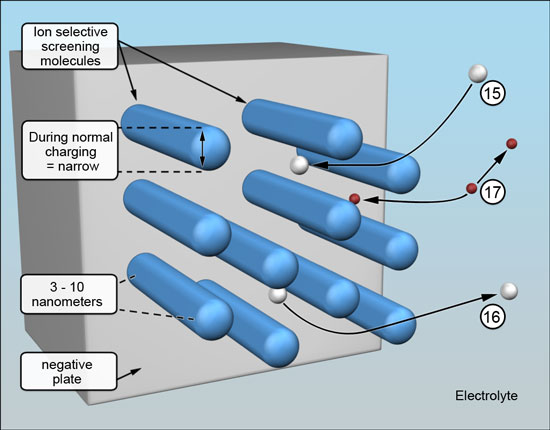
|
The barrier remains inactive while the battery is at rest, when it is discharging and is being charged - but not quite fully charged. The spacing between the individual bristles will be wide enough for the battery process ions to move to the negative plate -15 and from the negative plate -16, and for the hydrogen ions to pass freely in both directions -17. (The mechanism of hydrogen ion migration being proton transfer, from water molecule to water molecule, a different proton being passed on very rapidly each time.) |
|
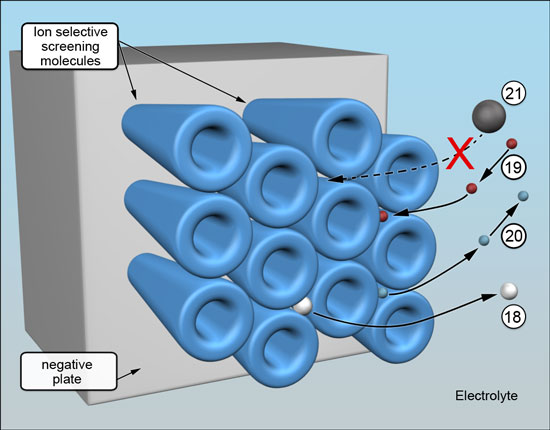
|
When the battery is being charged and is nearing full state of charge, there is the usual sharp increase in voltage and onset of gassing at 2.35 volts per cell. This increase also activates the barrier. Initially, during formation, at about 2.45 volts per cell the free ends of the bristles grow larger and increase in diameter, which results in the pathways between the electrolyte and the underlying negative plate becoming very much narrower. The threshold adjusts according to the rate of charging later - 2.22 for trickle, 2.30 for normal and 2.45 for fast charging.
The barrier remains porous. As charging nears completion, the last few remaining battery process ions emerge -18. The individual pathways achieve their optimum size by "squeezing down" until a minimum sustainable threshold of hydrogen ion migration is reached. It happens across the entire barrier, ensuring the billions upon billions of pathways are all kept exactly uniform in size - large enough to allow hydrogen ions to pass -19 and for nanobubbles of hydrogen gas to emerge - 20, but too small for migrating metal ions to reach the negative plate -21. This is what causes the concentration of metal ions in the battery acid electrolyte to rise to saturation and, in turn, helps to preserve the positive plate. (Metal ions do not exist in solution by themselves but are encased by a small cloud of water molecules, making them effectively much larger and easy to stop,
The barrier can operate only when the battery is on charge and is near or at full state of charge. It significantly increases the on-charge negative electrode (plate) potential, resulting in less gassing and a reduction in water consumption.
Saturation of the bulk of the battery acid electrolyte with metal ions provides a small reduction in the relative potential of the positive electrode (plate) which can sometimes help reduce charging times.
Electrical testing and teardowns confirmed the essential spongy pore texture of the active mass in the negative plates to be unaffected by the low dosage ion selective screening substance.
REFERENCES
PAUNOVIC, M and SCHLESINGER, M. "Fundamentals of Electrochemical Deposition", The Electrochemical Society, Inc., (John Wiley & Sons, New York, 1998), Reference 1, Chapter 10 section 2; Reference 2, Chapter 2 section 8. |
|
|
ION SELECTIVE SCREENING: CUTTING DOWN ON POSITIVE GRID CORROSION
The metal ion barrier can pave the way for thinner positive plates without attendant loss in battery life. The following is a more detailed explanation of the sequence of electrochemical and physical interactions that began with the formation of the electrochemical barrier over the surfaces of the negative plates - and ends up helping to reduce positive grid corrosion.
The working potential required to bring about electroplating of lead is very low, a potential of only 0.1 to 0.5 volts per cell is typically all that is required for the operation of lead electroplating baths of the type used by the electrorefining and electroplating industries.
In electroplating, metal of a positive electrode is progressively dissolved into a suitable electrolyte and is plated out onto a negative electrode under the influence of an electric current.
Since in principle, there is very little that distinguishes electroplating cells from lead-acid battery cells, this would seem to imply that at over 2.0 volts per cell, electroplating should be taking place in every lead-acid battery cell at a veritable hurricane force rate.
It is well known that this simply does not happen. It does not happen mainly because the solubility of lead in sulfuric battery acid is extremely low. The electric field that is trying to "drag" lead metal away from the surface of the positive plate grids is in no way diminished by this low solubility, however.
Electrolysis, (gassing charge), is an essential participant but solvation of the lead is the initiator of corrosion. Corrosion quickly covers the surfaces of the lead conductors and support structures of the positive plates with a protective layer of lead dioxide, Pb02. The layer has semi permeable properties. |
|
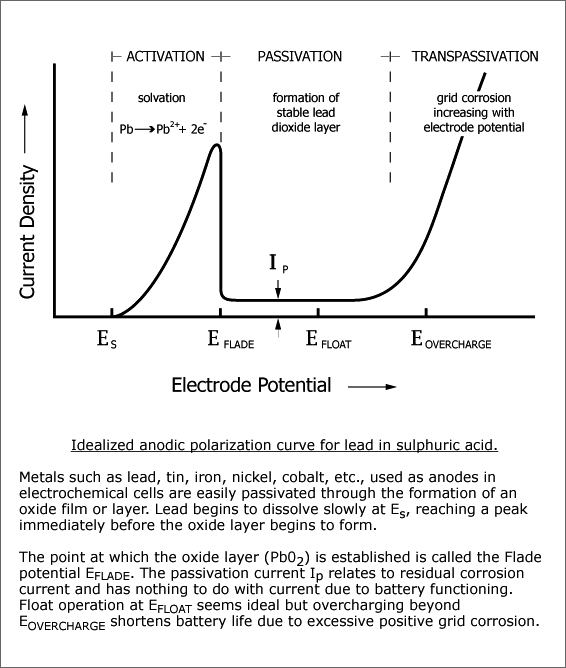
|
For batteries used on float duty, the layer is sufficient to further reduce electroplating to an imperceptible level.
During overcharging significant amounts of lead metal underlying the lead dioxide layer become partially dissolved, thus able to migrate via the semi permeable layer of lead dioxide, to the surface of the protective layer, whereupon most of the lead becomes fully solvated and converted to lead dioxide which precipitates onto the protective layer. Over time this results in failure of the positive plates through plate growth, grid disintegration and sludging of the active mass. The balance electroplates out onto the negatives, causing mossing and "leading" through, (Pb-ing).
The negative plates act as powerful scavengers during overcharging. They extract lead ions from the electrolyte and thereby reduce the already low lead concentration to a very low concentration. This helps the electric field to draw lead away from the conductors and support structures of the positive plates during overcharging.
Flat plate pasted positives are especially prone to this effect. In the case of tubular positives, the volume of lead dioxide active material that surrounds the spines helps to attenuate migration of the lead out of the underlying metal spines.
When the metal ion barrier is present, the lead ions that would otherwise have been electroplated onto the negative plates, are
no longer able to do so as before. The concentration of lead in the bulk of the electrolyte is able to rise to saturation. Importantly, there is not enough lead to return to the positives to make a difference.
The upshot is that the negative plates, which had been behaving
as powerful attractors to the lead ions, albeit via a difficult-to-negotiate path, would no longer be able to exert their previous influence. This would be followed by a steep decrease in the rate of dissolution of the structural lead and a corresponding reduction
in the precipitation of lead dioxide.
In a nutshell, regulation of a few ions that are flowing via a difficult-to-negotiate path and subject to a powerful electric field provides control over the flow of numerous partially dissolved ions that are following an easy-to-negotiate route. This amounts to a form of amplification. The ions can include lead, antimony, tin, etc. |
|
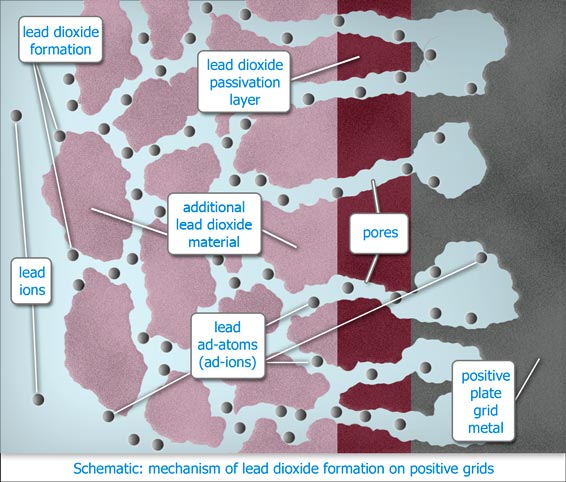

|
The benefits can be very significant. The rate of corrosion during moderate overcharging can be brought in line with float duty corrosion. The severe corrosion that accompanies excessive overcharging is unlikely to result in premature failure of the battery. The onset of positive plate growth and sludging can
be delayed.
The unusual combination of materials and interactions appears to have contributed to the metal ion barrier having been long overlooked in the context of lead-acid batteries.
This is not about a theory but a technology that has undergone field trials. It is about extensive Faraday-style investigative experimentation that positively identified the mechanism at work and helped to develop the best materials for the job.
It has taken the convergence of knowhow in such diverse fields as battery and electroplating technology, plus semiconductor experience, against a background of physics to recognize what it is, what it can do and how to harness it. |
|
|
 |
|